Lamination protects your Phaser 600 prints from scratches, damage, and wear from extensive handling. Lamination also enhances image quality and provides an attractive finish. You can protect your wide-format prints using commercially available, pressure-sensitive and warm-temperature (under 200° F) lamination film. For best lamination performance, Xerox offers lamination film specially formulated for Xerox ColorStix solid ink and designed to produce high quality, durable laminated prints.
This paper introduces the basics of laminating Phaser 600 prints and presents useful hints for avoiding problems with lamination.
Some Phaser 600 users are concerned that solid ink prints do not laminate well, because of the relatively low melting temperature of the ink (approximately 200° F; 93° C). In fact, when the laminator speed is properly adjusted, the solid ink does not reach it's melting temperature, even at lamination temperatures of 200° F (93° C).
You can use Xerox lamination film to laminate Phaser 600 prints on any commercially available heat/pressure laminator that meets the specifications listed in the following table. Xerox lamination film has been successfully tested using the Pro-Tech FALCON laminator. However, you can obtain good results with any laminator that meets the specifications in the table. Laminators are also available from Seal, Sallmetall, and others.
Feature
|
Specification
|
Roll size
|
37 inches (940 mm) wide
6.8 inches (173 mm) outside diameter
|
Upper pressure roller temperature
|
180° - 200° F (82° - 93° C)
|
Lower pressure roller temperature
|
Ambient
|
Laminator speed
|
0.5 - 0.75 inches (12.70 - 19.05 mm) per second
|
Nip pressure
|
Minimum setting for best print quality
|
Take-up spool
|
Requires release liner take-up spool
|
- Setting the printer's fusing mode to Cold or Hot makes the prints more resistant to damage from handling prior to lamination.
- Warm up the laminator completely before laminating prints.
- If the laminator is equipped with cooling fans, use them to reduce the possibility of curled prints.
- Set the laminator's nip pressure low enough to avoid ink smear and possible damage to laminator pressure rollers.
- For paper prints, use Xerox Smooth White Bond or Photo Grade Presentation papers and Xerox Lamination Film for best results.
- For extra-durable or special purpose uses, you can laminate prints made on these Xerox media: Premium Tracing/Backlit Paper, Transparent Film, Backlit Display Film, and Repositionable Adhesive Display Vinyl.
- Lamination of canvas material is not recommended.
- For lamination supplies ordering information, see Ordering lamination supplies.
One side or both?
You may want to experiment with laminating both sides of your prints. Laminating both sides provides two important advantages:
- Prints are more rigid and more durable, with less curl.
- Prints are more resistant to color fading.
Lamination and color fading
Color stability can vary by more than a factor of 0.5X - 2X, depending on environmental factors, such as temperature, amount and intensity of light, and orientation.
Without lamination, Phaser 600 colors are stable for about one year indoors and three weeks outdoors, in typical environments. Testing at Xerox has shown that lamination can improve color stability by 20% (your results may vary depending on environmental factors).
To get the best color stability improvements from lamination, laminate prints on both sides, or make your laminated prints on vinyl, transparency film, or backlit film. It also helps to make sure that laminated prints have a margin, ensuring that all edges are completely sealed.
Lamination is an interaction between laminator speed, heat, and pressure. To get the best results, it is important to adjust your laminator properly. This may require some experimentation for different type of prints.
To understand lamination, let's first look closely at a piece of lamination material, then we'll learn a little about how the lamination process works.
This diagram represents an enlarged cross-section of a piece of lamination material. It consists of a sheet of clear, protective film (PET substrate), a layer of adhesive, and a sheet of release liner. The release liner prevents the lamination material from sticking to itself during shipment.
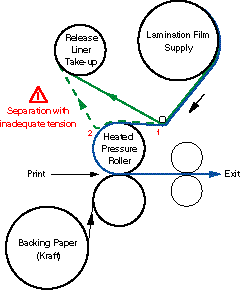
During the lamination process, the release liner is separated from the lamination film (1) just before the material comes in contact with the heated pressure roller. The material is then pressed against the print as they pass between the two pressure rollers. The heat melts the adhesive and the pressure seals the substrate of protective film to the print.
Poor bonding between the lamination film and the print can result from insufficient tension on the release liner take-up spool. This causes the release liner to separate incorrectly (2), leaving some of the adhesive on the release liner. Insufficient adhesive can cause a weak bond between the lamination material and the print. To avoid this problem, make sure that the tension on the release liner take-up spool is adequate.
Colors look melted after lamination
Either the temperature is too hot or the speed too slow, or both. The best speed depends on the thickness and density of the print. To test for the best temperature and speed combination, set the temperature, then try laminating several copies of the same print, slowing down the speed a little each time until the colors begin to look melted. Then increase the speed until the melting is eliminated. This is the best setting for that print.
Either the temperature is too cold or the speed too fast, or both. This is the opposite of the previous problem (melting); use the method given there for finding the best temperature/speed combination.
On single-sided laminations, back up the print with a blank sheet of paper that is slightly larger than the print. This will absorb excess adhesive at the edges. After laminating several prints, you can feed a blank sheet of paper through the laminator to pick up traces of excess adhesive from the rollers.
The best way to remove adhesive from the edges of laminated prints is with 90% isopropyl alcohol and a clean, lint-free, cloth. You can also remove adhesive from laminator rollers with a clean, lint-free cloth, but consult your laminator's user manual for the recommended cleaning fluid.
Lamination film may not adhere equally to all colors. Heavy applications of solid, dark, colors could be trouble spots. In these cases, careful attention to the laminator adjustments could be required to acheive satisfactory results.
If there is a region along the edge of the print that is not bonding well, make sure that the print has a margin, so that all edges are completely sealed.
Sometimes color areas, lines, or text develop a fuzzy or blurred appearance over time. This is known as color bleeding. To reduce bleeding, try using a different lamination film; contact the film manufacturer for more information. For best results, use Xerox lamination film.
To order supplies, contact your local dealer or, in the United States, call Xerox at 1-800-835-6100.
Item
|
Dimensions
|
Order number
|
High Gloss Lamination Film
|
940 mm x 76.2 m (37 in. x 250 ft.)
|
016-1496-00
|
Smooth White Bond Paper
|
610 mm x 60.9 m (24 in. x 200 ft.) 914 mm x 60.9 m (36 in. x 200 ft.)
|
016-1474-00 016-1475-00
|
Photo Grade Presentation Paper
|
610 mm x 45.7 m (24 in. x 150 ft.) 914 mm x 45.7 m (36 in. x 150 ft.)
|
016-1476-00 016-1477-00
|
Premium Tracing/Backlit Paper
|
914 mm x 45.7 m (36 in. x 150 ft.)
|
016-1478-00
|
Transparent Film
|
914 mm x 22.8 m (36 in. x 75 ft.)
|
016-1483-00
|
Backlit Display Film
|
914 mm x 15.2 m (36 in. x 50 ft.)
|
016-1479-00
|
Repositionable Adhesive Display Vinyl
|
914 mm x 15.2 m (36 in. x 50 ft.)
|
016-1481-00
|